What is Porosity in Welding: Comprehending Its Reasons and Enhancing Your Skills
What is Porosity in Welding: Comprehending Its Reasons and Enhancing Your Skills
Blog Article
Porosity in Welding: Identifying Common Issues and Implementing Ideal Practices for Avoidance
Porosity in welding is a prevalent concern that often goes undetected till it creates considerable problems with the integrity of welds. In this conversation, we will check out the vital aspects contributing to porosity development, examine its damaging effects on weld efficiency, and review the best practices that can be adopted to decrease porosity incident in welding procedures.
Usual Sources Of Porosity

Making use of filthy or damp filler materials can present pollutants right into the weld, adding to porosity problems. To reduce these typical causes of porosity, complete cleansing of base steels, correct protecting gas choice, and adherence to optimal welding parameters are necessary methods in accomplishing top quality, porosity-free welds.
Influence of Porosity on Weld Quality

The existence of porosity in welding can significantly compromise the structural integrity and mechanical homes of bonded joints. Porosity develops spaces within the weld steel, compromising its overall toughness and load-bearing capacity. These gaps function as stress focus points, making the weld extra vulnerable to fracturing and failing under used lots. Furthermore, porosity can lower the weld's resistance to rust and other environmental elements, even more diminishing its durability and efficiency.
One of the primary repercussions of porosity is a decline in the weld's ductility and toughness. Welds with high porosity degrees have a tendency to display reduced impact toughness and lowered ability to deform plastically prior to fracturing. This can be specifically worrying in applications where the welded elements are subjected to dynamic or cyclic loading problems. Porosity can hinder the weld's capacity to efficiently transfer forces, leading to premature weld failure and possible safety and security risks in essential structures. What is Porosity.
Best Practices for Porosity Prevention
To improve the architectural stability and top quality of welded joints, what particular actions can be executed to lessen the incident of porosity throughout the welding process? Making use of the right welding technique for the particular material being welded, such as changing the welding angle and weapon setting, can even more avoid porosity. Regular evaluation of welds and prompt removal of any type of concerns recognized throughout the welding procedure are important methods to avoid porosity and create top quality welds.
Importance of Proper Welding Methods
Applying proper visit our website welding techniques is vital in making certain the structural stability and top quality of welded joints, building on the structure of efficient porosity avoidance measures. Welding methods straight impact the total toughness and durability of the welded structure. One essential aspect of proper welding techniques is maintaining the right warm input. Extreme warm can result in raised porosity due to the entrapment of gases in the weld pool. Conversely, not enough heat might cause incomplete combination, producing prospective weak points in the joint. In addition, utilizing the appropriate welding criteria, such as voltage, existing, and take a trip rate, is important for attaining sound welds with marginal porosity.
Additionally, the selection of welding procedure, whether it be MIG, TIG, or stick welding, ought to align with the particular requirements of the task to make sure optimal results. Proper cleaning and prep work of the base metal, in addition to choosing the appropriate filler material, are additionally essential parts of skillful welding techniques. By sticking to these finest methods, welders can decrease the danger of porosity development and produce high-grade, structurally audio welds.
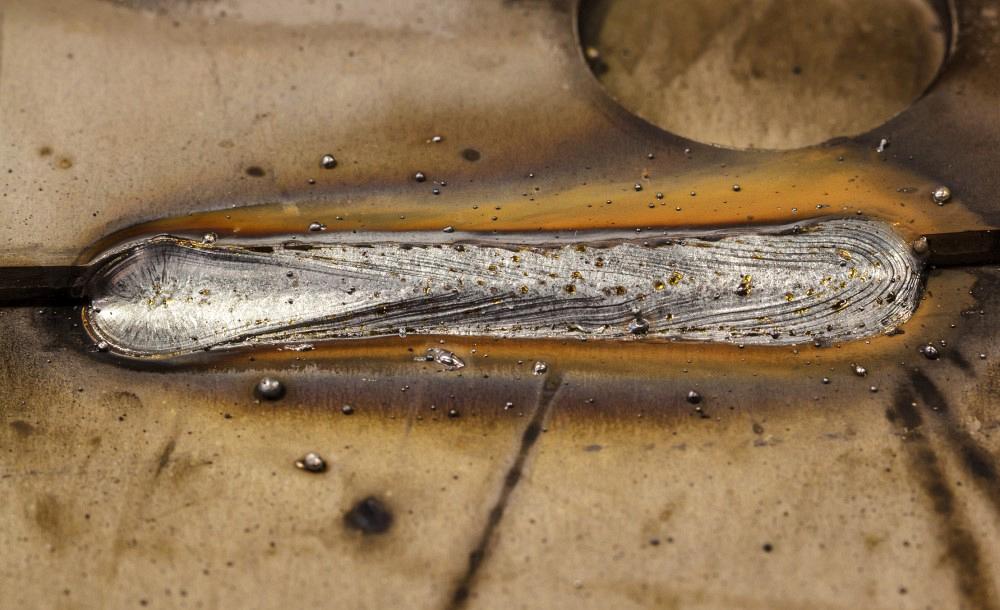
Examining and Quality Assurance Steps
Quality assurance steps play a vital function in confirming the stability and reliability of welded joints. view it now Testing procedures are vital to spot and stop porosity in welding, guaranteeing the stamina and longevity of the last item. Non-destructive screening techniques such as ultrasonic testing, radiographic screening, and aesthetic inspection are frequently utilized to determine potential problems like porosity. These techniques permit the evaluation of weld top quality without compromising the stability of the joint. What is Porosity.
Performing pre-weld and post-weld examinations is likewise vital in maintaining quality assurance criteria. Pre-weld inspections entail confirming the products, tools setups, and tidiness of the workplace to avoid contamination. Post-weld assessments, on the various other hand, evaluate the final weld for any issues, including porosity, and confirm that it satisfies specified standards. Executing a detailed quality assurance plan that includes comprehensive screening procedures and evaluations is vital to decreasing porosity issues and ensuring the overall quality of welded joints.
Verdict
To conclude, porosity in welding can be a common problem that influences the high quality of welds. By recognizing the usual sources of porosity and executing best methods for avoidance, such as correct welding methods and screening actions, welders can make go to this site sure excellent quality and reputable welds. It is important to prioritize prevention approaches to minimize the incident of porosity and preserve the stability of welded frameworks.
Report this page